3D45 Extruder
- Unclogging Extruder
- Replace Runout Sensor
- Nozzle Gap Calibration
Unclogging the 3D45 Extruder
This page will walk you through the steps to properly clear out a clogged extruder.
Since the reason the extruder may be clogged is not yet clear, the video will provide a several options to help you clear out the clog. You can also download the PDF instructions here.
Instruction
This document will outline the steps necessary to clear a clog in the heatsink tube assembly caused by the filament bulging up inside the tube. If the filament becomes clogged, neither loading nor unloading will be possible. Tube clogging can occur by either using an old filament that’s kept in the open for a longer duration or from 3rd party filaments with lower transition temperatures
Tools Required
• Unclog tool
• Brush
• Scissors
• Pliers
• 2mm Hex bit or Hex wrench (Allen key)
• 2.5mm Hex bit or Hex wrench (Allen key)
• T10 Torx bit or screwdriver (no longer than 4 inches).
TIP
In order to help avoid clogging please follow the recommendations below.
1. Only use Dremel filament.
2. Always unload the filament from the printer when not in use.
3. Always wait for the extruder to cool down see thermometer icon on screen empty.
4. Store your filament in a dry environment with a desiccant bag and clip the free end of the filament to the two holes in the spool to prevent filament getting tangled or brittleness.
Please call Dremel service center for help in unclogging your extruder.
Option A) Purge Filament

1. Pre-heat the extruder, go to Tools/Pre-heat. Wait until the extruder reaches the recommended temperature for your filament then click on purge when the icons turns green. Check for filament extruding. If there is no filament coming out your nozzle, please go to the next step.
2. Go to filament, select edit/view settings and increase the temperature of the extruder by 10°C go back to preheat and purge. Check for filament extruding. If there is no filament coming out your nozzle, please go to step X.
Tip: A good way to speed up the pre-heat process of the extruder is to click the pause icon on the screen for the platform temperature, this will allow your 3D printer nozzle to heat up faster.
Option B) Pull Filament
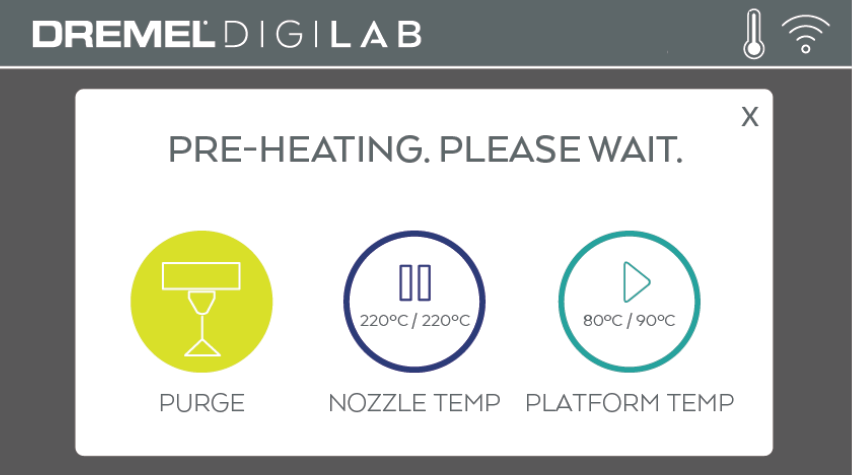
1. Pre-heat the extruder, go to Tools/Pre-heat. Wait until the extruder temperature reaches the recommended temperature for your filament.
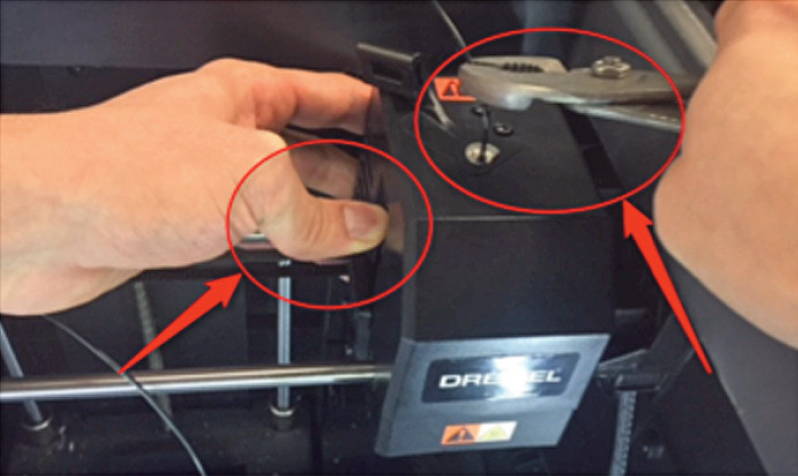
2. Grab the filament end that is available with the pliers, push on the side lever in the extruder to release tension on the filament and pull the filament at the same time with pliers.
Option C) Push Filament
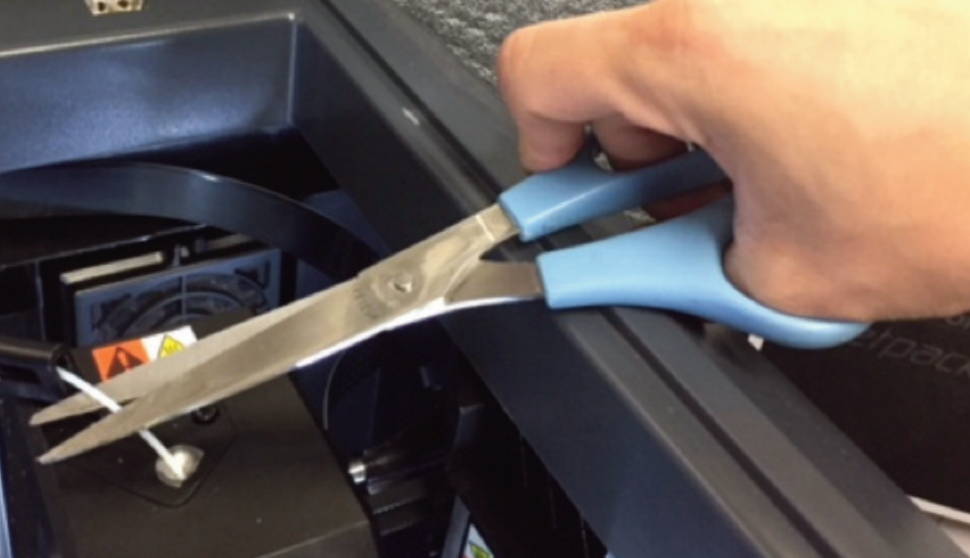
1. Cut filament.

2. Pre-heat the extruder, go to Tools/Pre-heat. Wait until the extruder temperature reaches the recommended temperature
for your filament.
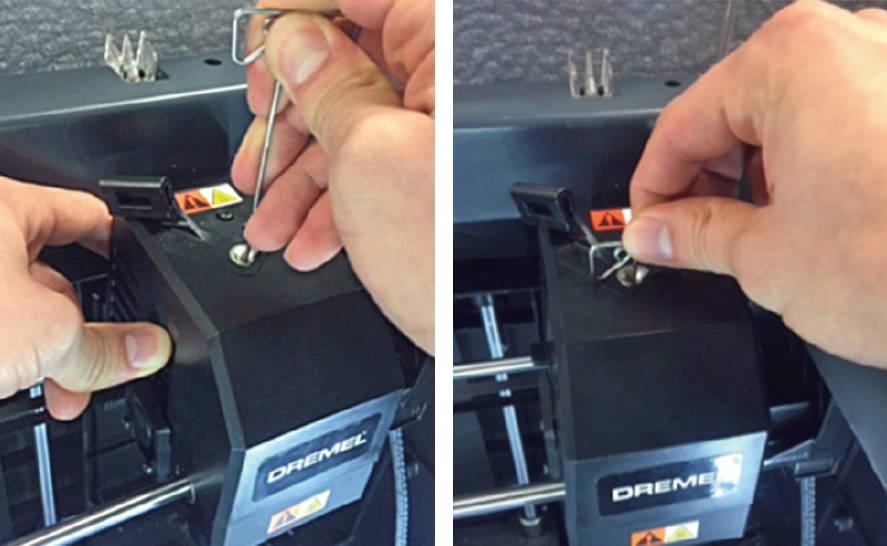
3. Push down on the lever on the side of extruder to release tension on the filament, and push the filament with a light force using the unclog tool. Check for filament extruding.
Option D) Check for Clogs in Stepper Motor
Caution
Use proper anti-static precautions when performing this replacement.
Discharge static electricity before beginning. Work on a static-free surface.

1. Bring Printer to Safe State for Service.
a. Turn on the printer, and verify that the temperature icon reads cool (see thermometer icon empty), if it is not cool (full thermometer), allow adequate time for the nozzle and bed to cool.
b. Turn off the printer
c. Unplug the printer

2. Remove Top Cover on the Extruder.
a.Cut the filament just before the intake on the top of the
extruder.

b. Remove screw located on the right side of the hole using the T10 Torx screwdriver. The first picture above shows the location of the screw, the second picture a bottom view of the area where the screw is located, circled in red is the screw that needs to be removed.

c. Unscrew the two screws on the top of the filament guide bracket using the 2.5mm bit or Hex wrench
d. Remove the top cover.

e. Carefully unplug filament run out switch from the extruder circuit board, ensuring to pull from the plastic plug and not the wires; pulling the wires can damage the connection to the extruder.
Please see picture above.

3. Removing the Extruder Motor.
a. Disconnect the white extruder terminal block from the extruder connector as shown in the picture above. Ensure to grab the block and avoid pinching the wires.

b. Unscrew the two motor screws below using the Torx screwdriver, as shown in the picture above. Please ensure that the screws once fully unscrewed, should still be left inserted in the extruder chassis hole.

c. Pull the extruder motor assembly away from the printer (vertically) as shown in the picture above.

4.Cleaning the stepper gear. There might be filament residue in your stepper motor gear, use your brush to clean the gear of the stepper motor.
5 Replace extruder motor
a. Place the extruder motor on the chassis. Extruder motor screw holes should line up with holes in the chassis.
b.Tighten the two hex screws with 2.5mm Hex wrench. Refer picture under Step 3b.
c. Plug in the white terminal block on the extruder connector as shown in picture under Step 3a (encircled).
6 Replace Top Cover
a. Attach the filament runout switch wires of the cover to the extruder circuit board. Refer picture under Step 2d.
b. Place the new top cover over the extruder.
c. Replace the two 2mm screws onto the cover. Refer picture under Step 2c.
7 Test the Machine
a. Plug in and turn on the 3D45.
b. Navigate to “Filament” and follow the on screen instructions to load filament.
c. Build a file on the machine to ensure the 3D45 printer is working correctly.
Replacing Runout Sensor on the 3D45
In this page you will find the steps to replace the filament run-out sensor, follow the steps or download the PDF instructions here.
Tools Required
• T10 Torx bit or screwdriver (no longer than 4 inches).
Instructions
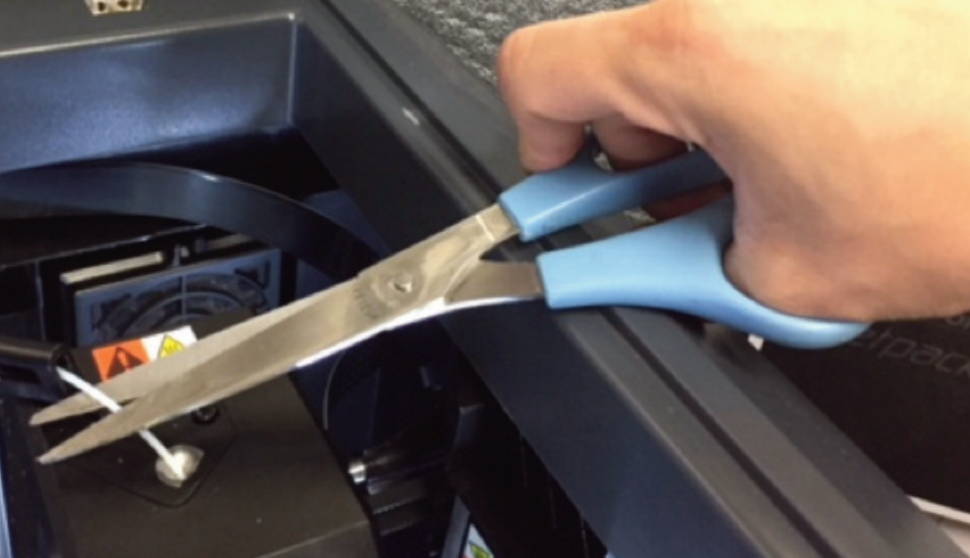
a. Cut the filament just before the intake on the top of the extruder.
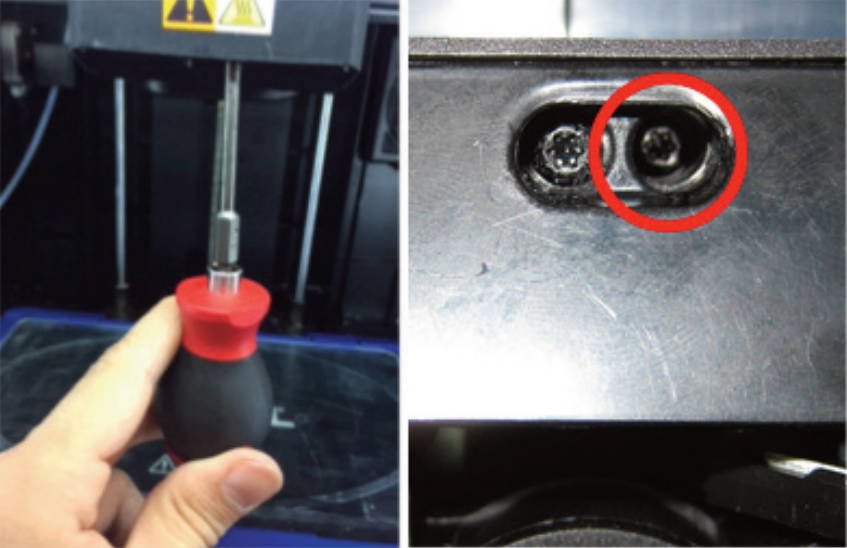
b. Remove screw located on the right side of the hole using the T10 Torx screwdriver. The first picture above shows the location of the screw, the second picture a bottom view of the area where the screw is located, circled in red is the screw that needs to be removed.
c. Unscrew the two screws on the top of the filament guide bracket usingthe 2.5mm bit or Hex wrench.
d. Remove the top cover.
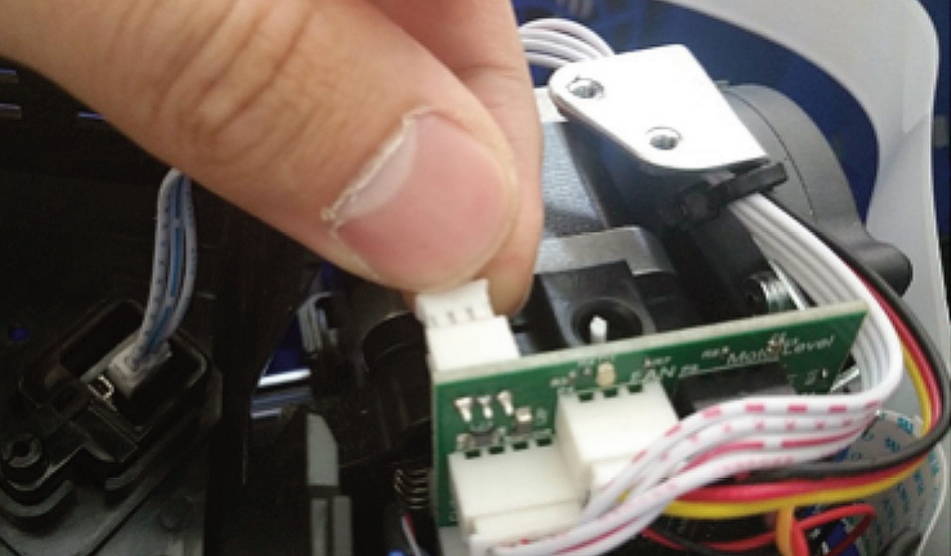
e. Carefully unplug filament run out switch from the extruder circuit board, ensuring to pull from the plastic plug and not the wires; pulling the wires can damage the connection to the extruder. Please see picture below.
Nozzle Gap Calibration
This video will walk you through the steps to modify your gap offsets and therefore achieve better print results. You can also download the PDF instructions here.
Having the correct nozzle gap is vital to achieving successful prints. The nozzle gap, also referred to as Z-Gap, is the distance of the nozzle to the build platform when the first layer is being printed. It is important to ensure that the first layer sticks well to the build platform, therefore, the nozzle gap needs to be ideal. Too large of a nozzle gap may lead to a not well adhered first layer, leading to object shifting, and a too small nozzle gap may lead to a non-visible first layer, possibly leading to clogging issues.
Instructions
Step 1: Go to Calibrate screen

From printer home screen, navigate to tools, calibrate, and then assisted nozzle calibration. Advanced users can use the nozzle gap calibration directly (non-assisted mode).
Step 2: Open Assisted Nozzle Calibration screen
a) Apply glue on the build platform. See glue application bulletin.
b) Ensure leveling switch is free of glue residue and that the filament has been loaded.
c) Level the build platform if needed.
Step 3: Assisted Nozzle Calibration

a. Nozzle will start heating up in order to perform the calibration.
b.In this process, three small rectangles will be printed side by side. Rectangle A will be printed with an offset of +0.1mm from the current setting, Rectangle B will be printed with no offset, and Rectangle C will be printed with a -0.1mm offset. An additional rectangle will be printed enclosing Rectangles A, B, and C in order to prime the nozzle and make sure filament is flowing correctly before starting the print.
Step 4: Nozzle Gap Calibration Analysis

a) Once the print has been completed, there will be three different rectangles representing three different Nozzle Gap offsets.
b) Look at rectangles A, B, and C to determine which offset has the best layer adhesion. Follow the instructions below for each scenario.

If you see little or no filament: If the nozzle is too close to the build platform, the first layer will print too tight to the build plate. Increase the Nozzle Gap +0.1mm. Repeat the Assisted Nozzle Calibration Process until an optimum nozzle gap has been achieved.

If the first layer is not adhering or gaps between the lines:If the nozzle is too far from the build plate, the first layer will not adhere well. Decrease the Nozzle Gap -0.1mm. Repeat the Assisted Nozzle Calibration Process until an optimum nozzle gap has been achieved.

Ideal nozzle gap distance:First layer will be adhering and be visible. Lines should not look like they were pressed against the build platform.